起きていた問題
透明プラスチック成形を強みにもつ製造業が、受注生産が拡大している中で品質不良数が増えていることを親会社から指摘され品質不良数を削減することを求められました。主な品質不良の要因を探索するともに、改善できる対策を模索しました。
コンサルタントの関わり方
品質不良の真の要因を分析し対策する
生産面と営業面から課題解決
・営業面から納得感のある限度見本を作成
・生産面から重要な品質不良の真因を探索し解決
・営業面から納得感のある限度見本を作成
・生産面から重要な品質不良の真因を探索し解決
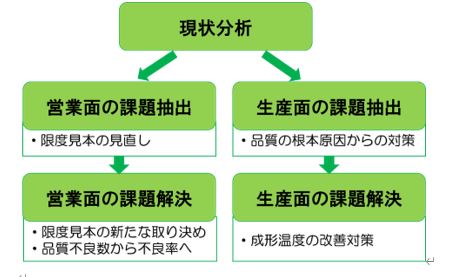
解決方法
生産面と営業面の両面から根本的に見直して品質改善
現状の分析として、社外クレームのみならず工程内不良も対象にして分析しました。社外に出る前の製品ついて工程内不良の根本原因を探索しました。営業面では限度見本がありましたが、さらに細かな限度見本を作成し、親会社が納得して取り決めを行うことで品質スペックの幅が広がりました。生産面ではQCストーリーの活用により、工程内不良の根本原因を見つけ出して改善しました。
解決 POINT 1
社外クレームに加えて、工程内不良を分析
社外クレーム、工程内不良についてABC分析しました。社外クレームでコンタミ不良が一番多いのが分かっていましたが、工程内で多いのはフラッシュ(蒸発分由来)やヤケであるのが判明し社長が意外な顔をされました。
解決 POINT 2
顧客・外注先に対して納得感のある限度見本を作成
営業面で品質の限度見本を確認させて頂きました。限度見本からコンタミがはみ出ないように品質検査を行っていることを確認しました。しかし、同じ面積で細長い異物や曲がりくねった繊維物は限度見本から外れてNG品扱いされていました。新たな限度見本を作成することによって、色々な面積基準に対応できるようになりコンタミ不良が改善しました。また親会社に品質不良数でなく品質不良率へ変更を交渉しました。交渉時では品質不良数のままでしたが、次回から品質不良率に変更されて、生産量が増えても品質不良率は増えなくなりました。
解決 POINT 3
重要な品質不良の真因を探索して課題解決
QCストーリーを用いてフラッシュとヤケの根本原因は、設備が老朽化し成形温度が想定温度に達していないことを突き止めました。QCストーリーは、①テーマの選択⇒②現状調査⇒③目標値の設定⇒④要因解析⇒⑤対策、処理⇒⑥効果の確認⇒⑦歯止め、まとめ、の順に誰にでも分かりやすく進める手法です。改善策としては射出成型機の先にノズルヒーターを設置し、金型に断熱版をつけて対応することによりフラッシュとヤケを改善しました。
効果・成果
営業面の限度見本作成と生産面のフラッシュとヤケについて、主要製品を改善しました。社外クレームの品質不良は5ヶ月後では最初の60%まで減少し、継続改善することで1年後には40%以下まで改善しました。
顧客へ納得感のある限度見本で交渉し、品質不良を真の原因を追究
製造業はきっちり生産して、顧客に販売できてこそ売上があがります。顧客に限度見本を提示して納得して頂いてこそ取引が続けられます。また社外クレームの前には、工程内クレームがあります。工程内クレームの真の原因をつかみ、対策することによって品質不良は減っていきます。社内では気づきにくいことも根本から分析いたしますのでお気軽にご相談下さい。